Phase formation and structure in rapidly quenched Ni50Al50 alloy
DOI:
https://doi.org/10.57056/ajet.v8i2.127Keywords:
SEM, XRD, NiAl, Alloy, NanoparticlesAbstract
A novel synthesis process combining arc melting and rapid quenched system has been developed to manufacture Ni50Al50 alloy which is not easy to form using conventional fabrication approaches. In this work, Nickel-Aluminum alloys with nominal composition Ni50at%Al50at% were prepared by melting pure nickel pieces (99.97%) and pure Al pieces (99.999%) under the protection of argon atmosphere using induction furnace followed by experiments performed by a new in-situ solidification method with arc melting. Alloy so produced is characterized by a compact structure with a minimum porosity. X-ray phase analysis revealed the existence of a one-phase structure of the rapidly quenched Ni50Al50 alloy. In this study, rapid quenching in liquid nitrogen from a high-temperature (1638 °C) state resulted in a non-uniform grain size distribution for Ni50Al50 alloy. Some grains were as small as 20 nm, while larger grains reached about 100 nm, with an average diameter of 74.8 nm. In contrast, cast ingots made with an induction furnace had larger average grain sizes (160-600 nm). These findings demonstrate the potential to create nanocrystalline structures in the Ni50Al50 alloy through rapid solidification in liquid nitrogen, offering the possibility of milling the synthesized alloy into nano-powders for composite matrix use during sintering. The nano-structuration behaviors and microstructures for Ni50Al50 alloy synthesis and powders nanoparticles obtained by milling have been investigated with the aids of Optical Microscopy (OM), X- Ray Diffraction (XRD) and Scanning Electron Microscopy (SEM).The results show that the samples rapidly quenched in liquid nitrogen from high temperature as solidus state with temperature slightly lower than 1638°C, restrain the precipitation of NiAl phase as clusters, consequently, the NiAl specimens above solidus follow by rapidly quenched in liquid nitrogen among NiAl nanoparticles make the phase distributes homogeneously.
References
Miracle DB. The physical and mechanical properties of NiAl. Acta Metall. Mater, 1993; 41: 649–684.
Clarke DR, Levi CG. Materials design for the next generation thermal barrier coatings. Annu. Rev. Mater. Res. 2003; 33: 383–417.
Wood JH, Goldman EH. High-temperature materials for aerospace and industrial power, in Superalloys II, C.T. Sims, N.S. Stoloff, Hagel WC.(eds), John Wiley & Sons Inc., New York, 1987; 359–384.
Williams JC, Starke A E. Progress in structural materials for aerospace systems, Acta Mater, 2003, 51(19):5775-5799.
Sun L, Simm TH, Martin TL, McAdam S, Galvin DR, Perkins KM, Bagot PAJ Moody MP, Ooi SW, Hill P, Rawson MJ, Bhadeshia HKDH. A novel, ultra-high strength maraging steel with balanced ductility and creep resistance achieved by nanoscale b-NiAl and Laves phase precipitates, Acta Materialia, 2018; 1491: 285-301.
Bochenek K, Basista M, Advances in processing of NiAl intermetallic alloys and composites for high temperature aerosapce applications. Progress in Aerospace Sciences, 2015; 79:136-146.
Barett CA. Effect of 0.1 at.% Zirconium on the Cyclic Oxidation Resistance of b- NiAl. Oxid. Met, 1988, 30: 361-390.
Miracle DB, Dariola R. Intermetallic Compounds, Practice, J.H. Westbrook, R.L. Fleischer, Ed., Wiley, New York, 1995; 2:55-74.
Cui HZ, Ma L, Cao LL, Teng FL, Cui N. Effect of NiAl content on phases and microstructures of TiC-TiB2-NiAl composites fabricated by reaction synthesis. Trans. Nonferr. Met. Soc. China 2014; 24: 346–353.
Pettit FS. Oxidation mechanisms for nickel-aluminum alloys at temperatures between 900◦ and 1300◦C. Trans. Metall. Soc. AIME 1967; 239:1296–1305.
Jia Q, Li D, Li S, Zhang Z, Zhang N. High-Temperature Oxidation Resistance of NiAl Intermetallic Formed In Situ by Thermal Spraying. Coatings Journal, 2018; 292:1-16.
Zhang Y, Wang H, Zhang F, Lu X, Zhang Y, Zhou Q. Growth kinetics and grain refinement mechanisms in an undercooled melt of a CoSi intermetallic compound. Journal of Alloys and Compounds. 2019; 781: 13-25.
Feng LC, Chen Z, Fan Y, Zhang JY, Shen BL. Relation between undercooled solidification and solid-state grain growth accompanying dynamic segregation. Vacuum. 2019; 161: 71-80.
Perepezko JH. Kinetic process in undercooled melts. Materials Science and Engineering. 1997; A226-228: 374-382.
Perepezko J H. Solidification of highly supercooled liquid metals and alloys. Journal of non-crystalline Solids. 1993; 156-158: 463-472.
Urritia A, Tumminello S, Arico SF, Sommadossi S. Characterization of Al-Ni intermetallics around 30-60 at% for TLPB application. Calphad, 44, 108-113.
Xu Y, Kameoka S, Kishida K, M Demura A, Tsai P, Xu Y, Hirano T. Catalytic properties of Ni3Al intermetallics for methanol decomposition. Mater. Trans. 2004; 45: 3177-3179.
Xu Y, Yang J, Demura M. Toshiyuki Hirano, Yoshitaka Matsushita, Masahiko Tanaka Yoshio Katsuya, Catalytic performance of Ni–Al nanoparticles fabricated by arc plasma evaporation for methanol decomposition. International Journal of hydrogen Energy. 2014; 39- 2522: 13156-13163.
Wen C, et al. Processing of fine-grained aluminum foam by spark plasma sintering. Journal of Materials Science Letters.2003; 22: 1407−1409.
Ashby MF, Evans AG, Fleck NA, Gibson LJ, Hutchinson JW, Wadley HNG. Metal Foams: A Design Guide, Butterworth-Heinemann Publ. Elsevier. 2000.
Hull MS, Quadros ME, Born R, Provo J, Vinod K, Lohani V, Mahajan RL. Sustainable Nanotechnology: A regional Perspective. Nanotechnology Environmental Health and Safety. 2014; 395-424.
Santos MAF, Lobo IP, da Cruz RS. Synthesis and characterization of novel ZrO2-SiO2 mixed oxides. Mater. Res. 2014; 17: 700–707.
Fidelus JD, Lojkowski W, Millers D, Grigorjeva L, Smits K, Piticescu RR. Zirconia based nanomaterials for oxygen sensors–generation, characterisation and optical properties. Solid State Phenomena. 2007, 128: 141–150.
Pabi RJ, Murty BS. Mechanism of mechanical alloying NiAl and Cu-Zn systems materials. Science and Engineering. 1996; A 214: 146-152.
Gogebakam M, Uzun O, Karaashan T, Keskin M, Rapidly solidified Al-6.5wt%Ni Alloy. Journal of Materials Processing Technology. 2003; 142: 87-92.
Jayakumar S, Ananthapadmanabhan PV, Perumal K, Thiyagarajan TK, Mishra SC, Su LT, Tok AIY, Guo J. Characterization of nano-crystalline ZrO2 synthesized via reactive plasma processing. Materials Science and Engineering: B. 2011; 176(12): 894-899.
Thompson RJ, Zhao JC, Hemker KJ. Effect of ternary elements on a martensitic transformation in βNiAl, J. Intermetallics. 2010; 18: 796-802.
Colin J, Serna S, Campillo B, Flores O, Juarez-Islas J. Microstructural and lattice parameter study of as cast and rapidly solidified NiAl intermetallic alloys with Cu additions. J. Intermetallics. 2008; 16: 487-853.
Ozdemir O, Zeytin S, Bindal C. A study on NiAl produced by pressure assisted combustion synthesis. Vacuum. 2010; 84:430-437.
Bellezza F, Nocchetti M, Posati T, Giovagnoli S, Cipiciani A. Synthesis of colloidal dispersions of NiAl, ZnAl, NiCr, ZnCr, NiFe and MgFe hydrotalcite-like nanoparticles. Journal of Colloid and Interface Science. 2012; 376 (1): 20-27
Jorgensen DJ, Michael S, Pollock TM. Femtosecond laser ablation and nanoparticles formation in intermettalic NiAl. Applied Surface Science. 2015; 353: 700-707.
Saidi D, Zaid B, Boutarfaia S, Hadji S, Souami N, Bibérian JP. Formation of zirconium and nickel oxide nanoparticles via oxidation of quenched melted Ni-Zr alloys. Ceramics International. 2012; 38: 6957–6961.
Herlach D M, Galenko P. Rapid solidification: in situ diagnostics and theoretical modelling. Mater. Sci. Eng. A. 2007; 34-41: 449-451.
Herlach DM, Eckler K, Karma A, Schwarz M. Grain refinement through fragmentation of dendrites in undercooled melts. Mater. Sci. Eng. A. 2001, 20-25: 304-306.
Huang W, Chang YA. A thermodynamic analysis of NiAl system. Intermetallics. 1998, 6: 487-498.
Suryanarayana C, Ivanov E. Mechanochemical synthesis of nanocrystallinemetal powders. Advances in Powder Metallurgy. 2013, 42-68
Enami K, Nenno S, Shimizu K. Crystal Structure and Internal Twins of the Ni-36.8 at% Al Martensite. Transactions of the Japan Institute of Metals. 1973, 14(2): 161–165.
Ragupathi C, Vijaya JJ, Surendhar P, Kennedy LJ. Comparative investigation of nickel aluminate (NiAl2O4) nano and microstructures for the structural, optical and catalytic properties. Polyhedron. 2014, 72: 1–7.
Sun Y, Lin P, Yuan SJ. A novel method for fabricating NiAl alloy sheet using laminated Ni/Al foils. Mater. Sci. Eng. A. 2019, 754: 3428-436.
Ozdemir O, Zeytin S, Bindal C. Characterization of two-phase nickel aluminides produced by pressure-assisted combustion synthesis. Vacuum. 2008, 82: 311–315.
Povarova KB, Skachkov OA. Preparation, Structure, and Properties of Ni3Al and NiAl Light Powder Alloys for Aerospace. Materials Science Forum. 2007; 534-536: 1585-1588.
Fragea N, Kalabukhova S, Wagnera A, Zaretskyb EB. High temperature dynamic response of SPS-processed Ni3Al., Intermetallics.2018; 102: 26-33
Shevtsova L, Mali V, Bataev A, Anisimov A, Dudina D. Microstructure and mechanical properties of materials obtained by spark plasma sintering of Ni3Al–Ni powder mixtures. Materials Science & Engineering A. 2020; 773: 138882.
Schryvers D, Ma Y, Toth L, Tanner L. Electron microscopy study of the formation of Ni5Al3 in a Ni62.5Al37.5 B2 alloy—I. Precipitation and growth. Acta Metallurgica et Materialia. 1995; 43: 4045-4056.
Schryvers D, Ma Y, Toth L, Tanner L. Electron microscopy study of the formation of Ni5Al3 in a Ni62.5Al37.5 B2 alloy—II. Plate crystallography. Acta Metallurgica et Materialia. 1995; 43: 4057-4065.
Schryvers D, Moritz DH. Austenite and martensite microstructures in splat-cooled NiAl. Intermetallics. 1998; 6: 427-436.
Zhang ZX, Jiang H, Russell AM, Skrotzki W, Müller E, Schneider R. Microstructural evolution and phase transformation in the liquid-solid Al/Ni diffusion couple. Philosophical Magazine. 2019; 99:1103-1120.
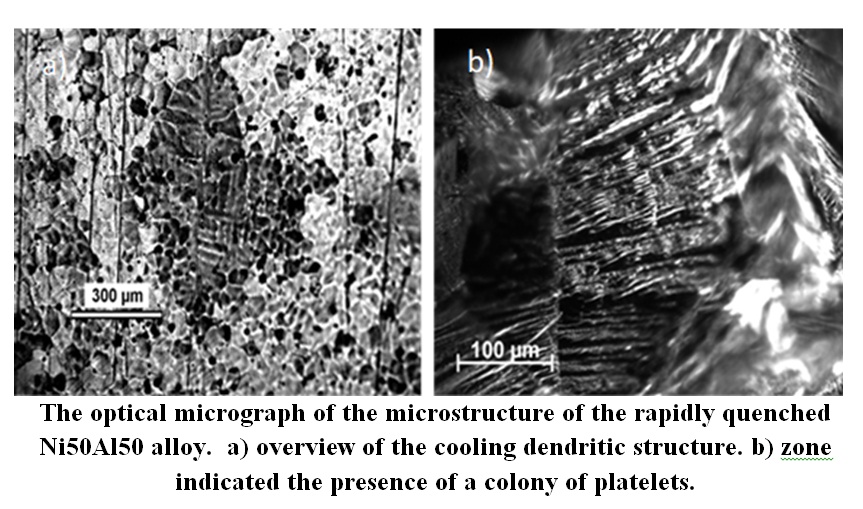
Downloads
Published
How to Cite
Issue
Section
License
Copyright (c) 2023 Youcef Khenioui, Djaffar Saidi, Bachir Zaid, Mohamed Sadouki, Nassim Souami, Badis Rahal

This work is licensed under a Creative Commons Attribution-NonCommercial 4.0 International License.